De material som vanligtvis används vid plåtbearbetning är kallvalsad platta (SPCC), varmvalsad platta (SHCC), galvaniserad platta (Secc, SGCC), koppar (Cu) mässing, röd koppar, beryllium koppar, aluminiumplatta (6061, 5052) 1010, 1060, 6063, duralumin, etc.), aluminiumprofiler, rostfritt stål (spegel, borstad, matt), beroende på produktens roll, är valet av material annorlunda och måste i allmänhet beaktas från produktens användning och kostnad.
1. Kallrullat ark SPCC används huvudsakligen för elektroplätering och bakningslackdelar, låg kostnad, lätt att forma och materialtjocklek ≤ 3,2 mm.
2. Hot-rullat ark SHCC, material T≥3,0 mm, använder också elektroplätering, bakningslackdelar, låga kostnader, men svåra att bilda, främst platta delar.
3. Galvaniserat ark SECC, SGCC. SECC -elektrolytiskt kort är uppdelat i N -material och P -material. N Material används huvudsakligen för ytbehandling och höga kostnader. P -material används för sprayade delar.
4. Koppar; använder huvudsakligen ledande material, och dess ytbehandling är nickelplätering, kromplätering eller ingen behandling, vilket är kostsamt.
5. Aluminiumplatta; Använd vanligtvis ytkromat (J11-A), oxidation (ledande oxidation, kemisk oxidation), hög kostnad, silverplätering, nickelplätering.
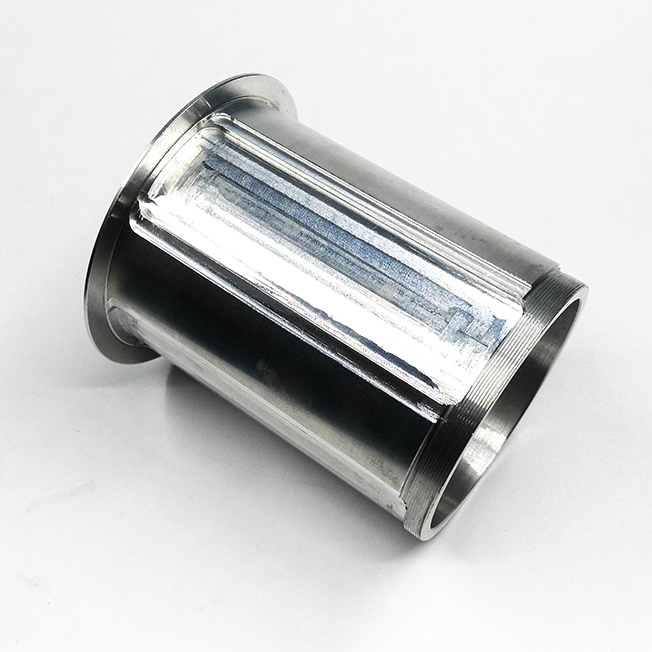
6. Aluminiumprofiler; Material med komplexa tvärsnittsstrukturer används ofta i olika underlådor. Ytbehandlingen är densamma som aluminiumplattan.
7. rostfritt stål; Huvudsakligen används utan ytbehandling, hög kostnad.
Dragöversikt
För att sammanställa processflödet för en del måste vi först veta de olika tekniska kraven i delritningen; Då är ritningsgranskningen den viktigaste länken i sammanställningen av delprocessflödet.
1. Kontrollera om ritningen är klar.
2. Förhållandet mellan ritningen och vyn, oavsett om markeringen är tydlig och fullständig, och dimensionens enhet är markerad.
3. Montering av förhållanden, montering kräver viktiga dimensioner.
4. Skillnaden mellan den gamla och den nya versionen av grafiken.
5. Översättning av bilder på främmande språk.
6. Konvertering av tabellkontor.
7. Feedback och bortskaffande av ritningsproblem.
8. Material
9. Kvalitetskrav och processkrav
10. Den officiella frisläppandet av ritningarna måste stämplas med en kvalitetskontrolltätning.
Försiktighetsåtgärder
Den utvidgade vyn är en planvy (2D) som utvecklats baserat på delritningen (3D)
1. Utvecklingsmetoden ska vara lämplig och det bör vara bekvämt att spara material och bearbetbarhet.
2. Välj rimligt gap- och kantmetoden, t = 2,0, gapet är 0,2, t = 2-3, gapet är 0,5 och kantmetoden antar långa sidor och korta sidor (dörrpaneler)
3. Rimlig övervägande av toleransdimensioner: Negativ skillnad går till slutet, positiv skillnad går hälften; Hålstorlek: Positiv skillnad går till slutet, negativ skillnad går hälften.
4. Burr -riktning
5. Rita en tvärsnittsvy genom att rita tänder, trycka på nitning, riva, stansning av konvexa punkter (paket), etc.
6. Kontrollera material, tjocklek och tjocklekstolerans
7. För speciella vinklar beror den inre radien för böjvinkeln (i allmänhet r = 0,5) på försöksböjningen.
8. Platser som är benägna till fel (liknande asymmetri) bör markeras
9. Förstorade bilder ska läggas till där det finns fler storlekar
10. Det område som ska skyddas genom sprutning måste anges
Tillverkningsprocesser
Enligt skillnaden i strukturen för plåtdelar kan processflödet vara annorlunda, men det totala överstiger inte följande punkter.
1. Skärning: Det finns olika skärmetoder, främst följande metoder
①. Shearing Machine: Den använder en klippmaskin för att klippa enkla remsor. Det används främst för att förbereda och bearbeta mögelblanking. Den har låg kostnad och noggrannhet under 0,2, men den kan bara bearbeta remsor eller block utan hål och inga hörn.
②. Punch: Den använder en stans för att slå ut de platta delarna efter att ha utvecklat delarna på plattan i ett eller flera steg för att bilda olika materialformer. Dess fördelar är korta arbetstimmar, hög effektivitet, hög precision, låg kostnad och den är lämplig för massproduktion. Men för att utforma formen.
③. NC CNC Blanking. När NC -blanking måste du först skriva ett CNC -bearbetningsprogram. Använd programmeringsprogramvaran för att skriva den utdragna bilden i ett program som kan kännas igen av NC Digital Ritning Processing Machine. Enligt dessa program kan du slå varje bit på plattan ett steg i taget. Strukturen är en platt bit, men dess struktur påverkas av verktygets struktur, kostnaden är låg och noggrannheten är 0,15.
④. Laserskärning ska använda laserskärning för att klippa strukturen och formen på plattplattan på en stor platt platta. Laserprogrammet måste programmeras som NC -skärning. Den kan ladda olika komplexa former av platta delar, med hög kostnad och noggrannhet på 0,1.
⑤. Sågmaskin: Använd huvudsakligen aluminiumprofiler, fyrkantiga rör, ritrör, runda staplar etc. med låg kostnad och låg precision.
1. Montör: räknare, knackning, reaming, borrning
Motborrvinkeln är i allmänhet 120 ℃, används för att dra nitar och 90 ℃ som används för räknare och tappar tumbottenhål.
2. Flanging: Det kallas också hålekstraktion och hålfläns, vilket är att dra ett något större hål på ett mindre bashål och sedan knacka på det. Det bearbetas huvudsakligen med tunnare plåt för att öka dess styrka och antalet trådar. , För att undvika glidande tänder, som vanligtvis används för tunnplatttjocklek, normalt grunt flänsande runt hålet, är det i princip ingen förändring i tjockleken, och när tjockleken får tunnas med 30-40%, kan det vara 40-högt än den normala flänshöjden. För en höjd av 60%kan den maximala flänshöjden erhållas när tunnningen är 50%. När plattans tjocklek är större, till exempel 2.0, 2.5, etc., kan den tappas direkt.
3. Stansmaskin: Det är en bearbetningsprocedur som använder formformning. Generellt inkluderar stansning av bearbetning stansning, hörnskärning, blanking, stansning av konvexa skrov (stöt), stansning och rivning, stansning, formning och andra bearbetningsmetoder. Bearbetningen måste ha motsvarande behandlingsmetoder. Formen används för att slutföra operationerna, såsom stansning och tömande formar, konvexa formar, rivningsformar, stansformar, formar formar, etc. operationen ägnar huvudsakligen uppmärksamhet på position och riktning.
4. Trycknätning: När det gäller vårt företag inkluderar trycknätning huvudsakligen trycknötter, skruvar och så vidare. Den drivs av hydrauliskt trycknätmaskin eller stansmaskin, nitar den till plåtdelar och utvidgar spännande sätt, måste vara uppmärksam på riktning.
5. Böjning; Böjning är att fälla 2D -platta delar i 3D -delar. Bearbetningen måste slutföras med en fällbar bädd och motsvarande böjformar, och den har också en viss böjsekvens. Principen är att nästa snitt inte kommer att störa den första vikningen och störningen kommer att inträffa efter vikningen.
l Antalet böjremsor är 6 gånger tjockleken på plattan under t = 3,0 mm för att beräkna spårbredden, såsom: t = 1,0, v = 6,0 f = 1,8, t = 1,2, v = 8, f = 2,2 , T = 1,5, v = 10, f = 2,7, t = 2,0, v = 12, f = 4,0
l Klassificering av fällbara sängformar, rak kniv, scimitar (80 ℃, 30 ℃)
l När aluminiumplattan är böjd finns det sprickor, bredden på den nedre die -spåret kan ökas och den övre dynor kan ökas (glödgning kan undvika sprickor)
l frågor som behöver uppmärksamhet vid böjning: ⅰ ritning, obligatorisk platttjocklek och kvantitet; Ⅱ Böjningsriktning
Ⅲ Böjningsvinkel; Ⅳ Böjningsstorlek; Ⅵ Utseende, inga veck är tillåtna på elektropläterade krommaterial.
Förhållandet mellan böjning och trycknitningsprocess är i allmänhet den första trycknätningen och sedan böjning, men vissa material kommer att störa trycknätningen och sedan trycka på först, och vissa kräver böjningstryck som är rivet-då böjning och andra processer.
6. Svetsning: Svetsdefinition: Avståndet mellan atomerna och molekylerna i det svetsade materialet och Jingda -gitteret är integrerat
①klassificering: En fusionssvetsning: Argon bågsvetsning, CO2 -svetsning, gassvetsning, manuell svetsning
B Trycksvetsning: Spot Welding, Butt Welding, bulsvetsning
C -lastning: elektrisk kromsvetsning, koppartråd
② Svetsmetod: En CO2 -gasskyddad svetsning
b argonbågsvetsning
C Spot Welding, etc.
D Robotsvetsning
Valet av svetsmetod är baserat på faktiska krav och material. Generellt används CO2 -gasskyddad svetsning för svetsning av järnplattor; Argon bågsvetsning används för svetsning av rostfritt stål och aluminiumplatta. Robotsvetsning kan spara arbetstimmar och förbättra arbetseffektiviteten. Och svetskvalitet, minska arbetsintensiteten.
③ Svetsningssymbol: Δ Filletssvetsning, д, I-typ svetsning, v-typ svetsning, en-sida v-typ svetsning (V) V-typ svetsning med stumt kanter (V), fläcksvetsning (O), pluggsvetsning eller ve Slotsvetsning (∏), crimp-svetsning (χ), ensidig V-formad svetsning med trubbig kant (V), U-formad svetsning med trubbig, J-formad svetsning med trubbig, ryggskyddssvetsning, varje svetsning
④ Arrow Line och Joint
⑤ Saknade svetsning och förebyggande åtgärder
Spotsvetsning: Om styrkan inte räcker kan bulor göras och svetsområdet införs.
CO2 -svetsning: hög produktivitet, låg energiförbrukning, låg kostnad, stark rostmotstånd
Argon bågsvetsning: grunt smältdjup, långsam smälthastighet, låg effektivitet, hög produktionskostnad, volfram inkluderingsfel, men har fördelarna med bättre svetskvalitet och kan svetsa icke-järnmetaller som aluminium, koppar, magnesium, etc.
⑥ Anledning till svetsdeformation: Otillräcklig förberedelse före svetsning, måste lägga till fixturer
Förbättra processen för dålig svetsarmatur
Dålig svetssekvens
⑦ Svetsdeformationskorrigeringsmetod: Flamkorrigeringsmetod
Vibrationsmetod
Hamring
Konstgjorda åldrande