Play Metal Processing är en navteknik som plåtstekniker behöver förstå, och det är också en viktig process för plåtproduktformning. Bladbearbetning inkluderar traditionell skärning, tömning, böjnings- och formningsmetoder och processparametrar, samt olika kallstämpeldivstrukturer och processparametrar, olika utrustningsarbetsprinciper och driftsmetoder och ny stämplingsteknik. Och ny teknik. Delar av plåt kallas plåtbearbetning. BEAKNINGSPLÄGNING kallas plåtbearbetning. Specifikt, till exempel, användningen av plattor för att göra skorstenar, järnfat, bränsletankar, oljetankar, ventilationsrör, armbågar, armbågar, kvadrater, trattar, etc. Huvudprocesserna inkluderar skjuvning, böjning, formning, svetsning, riveting , etc. viss geometrisk kunskap. Slådelar är tunna plåtdelar, det vill säga delar som kan bearbetas genom stämpling, böjning, sträckning och andra medel. En allmän definition är en del med en konstant tjocklek under bearbetningen. Motsvarande gjutningar, förfalskning, bearbetningsdelar etc.
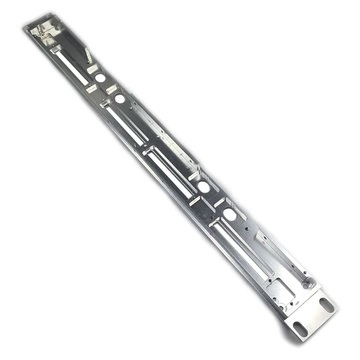
Varje bransch har sina professionella villkor, och arkningsindustrin är inget undantag. Följande 25 är vanliga.
(1) Trycknätning: hänvisar till processen med att krimpa fästelement som trycknötter, trycknitningskruvar eller trycknyckning av mutterstolpar på arbetsstycket med en stans eller hydraulisk press.
(2) Expandering av nitning: hänvisar till processen för första räknare och sedan använder du en stans eller en hydraulisk tryck för att fast krimpa den expanderande nitmuttern på arbetsstycket.
(3) Pullande mor: hänvisar till användningen av en liknande nitningsprocess. Processen att fast anslutning av anslutningar som Pop Rivet Nuts (POP) till arbetsstycket med en kvinnlig pistol.
(4) Pull nitning: avser processen att använda en nitande pistol som ett verktyg för att tätt ansluta två eller flera arbetsstycken med dragnaglar.
(5) Nitning: Processen att ansluta två eller flera arbetsstycken ansikte mot ansikte med nitar. För countersunk -nitning måste arbetsstyckena först skänks.
(6) Hörnskärning: avser processen att skära av hörnen på arbetsstycket med hjälp av en matris på en stans eller en hydraulisk press.
(7) Böjning: hänvisar till processen att bilda ett arbetsstycke av en böjmaskin.
(8) Formning: avser processen att deformera arbetsstycket med en form på en vanlig stans eller annan utrustning.
(9) Skärmaterial: hänvisar till den tekniska processen för att få ett rektangulärt arbetsstycke genom en klippmaskin.
(10) Blanking: hänvisar till den tekniska processen för arbetsstycket som skärs av laser eller stansad av CNC -stansmaskin.
(11) Blanking: avser processen att använda formar på vanliga stansar eller annan utrustning för att få produktformer.
(12) Stansning: hänvisar till den tekniska processen där arbetsstycket bearbetas av vanliga stansar och formar.
(13) Stansning av konvext skrov: avser processen att bilda en konvex form av ett arbetsstycke med en matris på en stans eller en hydraulisk press.
(14) Stansning och rivning: kallas också "stansbrygga", det hänvisar till processen att bilda ett arbetsstycke till en broliknande form med en matris på en stans eller hydraulisk press.
(15) Hålsuttag: även kallad "flänsning", som hänvisar till processen att bilda ett runt hål på ett arbetsstycke med en form på en gemensam stans eller annan utrustning. behandla.
(16) Tappning: hänvisar till processen för att bearbeta inre trådar på arbetsstycket.
(17) Utjämning: avser processen att använda annan utrustning för att jämna arbetsstycket före och efter att arbetsstycket är ojämnt.
(18) Trådning: hänvisar till processen för den andra trådåterställningen av det förfallna arbetsstycket.
(19) Borrning: avser den tekniska processen att borra ett arbetsstycke med en borrbit på en borrmaskin eller en fräsmaskin.
(20) Avfasning: hänvisar till processen för att bearbeta de skarpa hörnen på arbetsstycket med formar, filer, slipmaskiner etc.
(21) Stämpel: hänvisar till processen att stämpla ut karaktärer, symboler eller andra avtryck på arbetsstycket med en form.
(22) Motbor: avser processen att bearbeta avsmalnande hål på arbetsstycket för att matcha de anslutande delarna som liknar räknare.
(23) Plattning: avser processen för övergången från ett visst format arbetsstycke till plattning.
(24) Punching Mesh Hole: hänvisar till det nätliknande hålet som stansat ut på arbetsstycket med en matris på en vanlig stansmaskin eller en numerisk styrmaskin.
(25) Reaming: hänvisar till processen att bearbeta små hål på ett arbetsstycke i stora hål med en borrning eller frässkärare
Konstprocessredaktör
Urval
De material som vanligtvis används vid plåtbearbetning är kallvalsad platta (SPCC), varmvalsad platta (SHCC), galvaniserad platta (Secc, SGCC), koppar (Cu) mässing, röd koppar, beryllium koppar, aluminiumplatta (6061, 5052) 1010, 1060, 6063, duralumin, etc.), rostfritt stål (spegel, borstad, matt), enligt produktens olika funktioner, är valet av material olika och måste i allmänhet beaktas från produktens användning och kostnad .
1. Kallrullat ark SPCC används huvudsakligen för elektroplätering och bakningslackdelar, låg kostnad, lätt att forma och materialtjocklek ≤ 3,2 mm.
2. Hot-rullat ark SHCC, material T≥3,0 mm, använder också elektroplätering, bakningslackdelar, låga kostnader, men svåra att bilda, främst platta delar.
3. Galvaniserat ark SECC, SGCC. SECC -elektrolytiskt kort är uppdelat i N -material och P -material. N Material används huvudsakligen för ytbehandling och höga kostnader. P -material används för sprayade delar.
4. Koppar; använder huvudsakligen ledande material, och dess ytbehandling är nickelplätering, kromplätering eller ingen behandling, vilket är kostsamt.
5. Aluminiumplatta; Använd vanligtvis ytkromat (J11-A), oxidation (ledande oxidation, kemisk oxidation), hög kostnad, silverplätering, nickelplätering.
6. Aluminiumprofiler; Material med komplexa tvärsnittsstrukturer används ofta i olika underlådor. Ytbehandlingen är densamma som aluminiumplattan.
7. rostfritt stål; Huvudsakligen används utan ytbehandling, hög kostnad.
För processflödet av delen måste vi först veta de olika tekniska kraven i delritningen; Då är ritningsöversynen den viktigaste länken i sammanställningen av delprocessflödet.
1. Kontrollera om ritningen är klar.
2. Förhållandet mellan ritningen och vyn, oavsett om markeringen är tydlig och fullständig, och dimensionens enhet är markerad.
3. Monteringsförhållandet, montering kräver viktiga dimensioner.
4. Skillnaden mellan den gamla och den nya versionen av ritningen.
5. Översättning av bilder på främmande språk.
6. Konvertering av tabellkoden.
7. Feedback och bortskaffande av ritningsproblem.
8. Material.
9. Kvalitetskrav och processkrav.
10. De officiella frigöringsritningarna måste stämplas med en kvalitetskontrolltätning